Respect for People - 人資
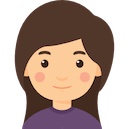
By Rachel
at 2007-12-21T04:43
at 2007-12-21T04:43
Table of Contents
與各位HR人分享一篇挺有意思的文章
轉錄自Lean Enterprise Institute的電子報
本文比較兩種協助員工解決問題的策略
For years I've visited companies where "respect for people" is a core element
of the corporate philosophy. So I've asked managers in many companies a
simple question. "How do you show respect?" I have usually heard that
employees should be treated fairly, given clear goals, trusted to achieve
them in the best way, and held to account for results. For example, "We hire
smart people, we give them great latitude in how they do their work because
we trust them, and we hold them to objective measures of performance. That's
respect for people."
When in recent years Toyota made respect for people one of the pillars of the
Toyota Way I decided I should ask the best Toyota managers how they show
respect for people. The answer I have heard is a good bit different from
what I’ve heard at many other companies and goes as follows:
Managers begin by asking employees what the problem is with the way their
work is currently being done. Next they challenge the employees' answer and
enter into a dialogue about what the real problem is. (It's rarely the
problem showing on the surface.)
Then they ask what is causing this problem and enter into another dialogue
about its root causes. (True dialogue requires the employees to gather
evidence on the gemba – the place where value is being created -- for
joint evaluation.)
Then they ask what should be done about the problem and ask employees why
they have proposed one solution instead of another. (This generally requires
considering a range of solutions and collecting more evidence.)
Then they ask how they – manager and employees – will know when the
problem has been solved, and engage one more time in dialogue on the
best indicator.
Finally, after agreement is reached on the most appropriate measure of
success, the employees set out to implement the solution.
For many of us that doesn't sound much like respect for people. The manager
after all doesn’t just say "I trust you to solve the problem because I
respect you. Do it your way and get on with it." And the manager isn’t a
morale booster, always saying, "Great job!" Instead the manager challenges
the employees every step of the way, asking for more thought, more facts,
and more discussion, when the employees just want to implement their
favored solution.
Over time I've come to realize that this problem solving process is actually
the highest form of respect. The manager is saying to the employees that the
manager can't solve the problem alone, because the manager isn't close enough
to the problem to know the facts. He or she truly respects the employees'
knowledge and their dedication to finding the best answer. But the employees
can't solve the problem alone either because they are often too close to the
problem to see its context and they may refrain from asking tough questions
about their own work. Only by showing mutual respect – each for the other
and for each other's role – is it possible to solve problems, make work
more satisfying, and move organizational performance to an ever higher
level.
Recently I walked through two distribution centers in the same city
providing the same type of service for their customers. As I walked
I found a wonderfully clear example of the difference that mutual
respect for people makes.
In the first facility management was focused on controlling the workforce
through individual metrics. Employees were told to get a given amount of
work done but given considerable latitude on just how to do it. They were
judged at the end of the day, week, month, and quarter on whether they
achieved the desired results, using data collected by a computerized tracking
system. Front-line managers were busily engaged in working around current
problems but none was systematically engaged in actually solving these
problems at the root cause in collaboration with the employees. This was a
task for higher-level managers and staff experts as time permitted, usually
without the involvement of the production associates.
In the second facility, the management had worked with employees to create
standard work for every task and had introduced visual control with status
boards so everyone could see how everyone else was proceeding with their
work. Because the condition of the entire process was instantly visible to
everyone, employees could help each other with any problems which emerged.
And because the work process was very stable due to strict adherence to
standardized work, line managers could devote most of their energy to problem
solving by engaging production associates in dialogues to get to root causes
and implement sustainable solutions. Indeed, every associate spent four hours
every week on improvement activities.
What is the result? Both facilities are in the same city, have employees with
the same educational level, and pay roughly the same wage. Yet annual turnover
of associates in the first facility is 70 percent (which seems to be typical
in distribution centers) and there is significant management turnover as well.
Meanwhile, in the second facility, associate turnover is 1 percent and
practically no managers leave. When I asked managers and associates in the
second center why this should be, the answer was simple: "The work here is
always challenging because we are always solving problems using a method we
all understand. And we all respect each other’s contribution."
The differences continue: In my rough estimate labor productivity in the second
facility is about twice that of the first even with less automation. This is
partly because the first facility is constantly hiring and training new
employees while the second distribution center spends practically no time
on this task. In addition, all employees in the second facility are experienced
and working at the top of their learning curve. Large amounts of confusion
about what to do next and larger amounts of rework are eliminated.
Finally, in the second facility, quality as experienced by customers is higher
as well even though there is less internal rework. And the total amount of
inventory on hand to provide the next-day service that both facilities promise
their customers is also much lower in the second distribution center.
I trust you can guess which facility is a Toyota parts distribution center and
which facility belongs to a distribution firm stuck (like most) in the age of
mass production with command-and-control management methods but little
discussion of how employees can best do their jobs.
I also trust that all of us want to show respect for people. The challenge for
those of us in the Lean Community is to embrace and explain the true nature of
mutual respect for people – managers and associates – so all organizations
can move toward a new and better way of solving their problems.
Best regards,
Jim
Jim Womack
Founder and Chairman
Lean Enterprise Institute
Feel free to forward this message to suppliers, customers, or colleagues who
are implementing lean - or should be.
If this e-letter was forwarded to you, visit http://www.lean.org to subscribe.
Just click the "Join" button on the right to get a free subscription and access
to all the valuable content about implementing lean principles in production
and service value streams.
--
轉錄自Lean Enterprise Institute的電子報
本文比較兩種協助員工解決問題的策略
For years I've visited companies where "respect for people" is a core element
of the corporate philosophy. So I've asked managers in many companies a
simple question. "How do you show respect?" I have usually heard that
employees should be treated fairly, given clear goals, trusted to achieve
them in the best way, and held to account for results. For example, "We hire
smart people, we give them great latitude in how they do their work because
we trust them, and we hold them to objective measures of performance. That's
respect for people."
When in recent years Toyota made respect for people one of the pillars of the
Toyota Way I decided I should ask the best Toyota managers how they show
respect for people. The answer I have heard is a good bit different from
what I’ve heard at many other companies and goes as follows:
Managers begin by asking employees what the problem is with the way their
work is currently being done. Next they challenge the employees' answer and
enter into a dialogue about what the real problem is. (It's rarely the
problem showing on the surface.)
Then they ask what is causing this problem and enter into another dialogue
about its root causes. (True dialogue requires the employees to gather
evidence on the gemba – the place where value is being created -- for
joint evaluation.)
Then they ask what should be done about the problem and ask employees why
they have proposed one solution instead of another. (This generally requires
considering a range of solutions and collecting more evidence.)
Then they ask how they – manager and employees – will know when the
problem has been solved, and engage one more time in dialogue on the
best indicator.
Finally, after agreement is reached on the most appropriate measure of
success, the employees set out to implement the solution.
For many of us that doesn't sound much like respect for people. The manager
after all doesn’t just say "I trust you to solve the problem because I
respect you. Do it your way and get on with it." And the manager isn’t a
morale booster, always saying, "Great job!" Instead the manager challenges
the employees every step of the way, asking for more thought, more facts,
and more discussion, when the employees just want to implement their
favored solution.
Over time I've come to realize that this problem solving process is actually
the highest form of respect. The manager is saying to the employees that the
manager can't solve the problem alone, because the manager isn't close enough
to the problem to know the facts. He or she truly respects the employees'
knowledge and their dedication to finding the best answer. But the employees
can't solve the problem alone either because they are often too close to the
problem to see its context and they may refrain from asking tough questions
about their own work. Only by showing mutual respect – each for the other
and for each other's role – is it possible to solve problems, make work
more satisfying, and move organizational performance to an ever higher
level.
Recently I walked through two distribution centers in the same city
providing the same type of service for their customers. As I walked
I found a wonderfully clear example of the difference that mutual
respect for people makes.
In the first facility management was focused on controlling the workforce
through individual metrics. Employees were told to get a given amount of
work done but given considerable latitude on just how to do it. They were
judged at the end of the day, week, month, and quarter on whether they
achieved the desired results, using data collected by a computerized tracking
system. Front-line managers were busily engaged in working around current
problems but none was systematically engaged in actually solving these
problems at the root cause in collaboration with the employees. This was a
task for higher-level managers and staff experts as time permitted, usually
without the involvement of the production associates.
In the second facility, the management had worked with employees to create
standard work for every task and had introduced visual control with status
boards so everyone could see how everyone else was proceeding with their
work. Because the condition of the entire process was instantly visible to
everyone, employees could help each other with any problems which emerged.
And because the work process was very stable due to strict adherence to
standardized work, line managers could devote most of their energy to problem
solving by engaging production associates in dialogues to get to root causes
and implement sustainable solutions. Indeed, every associate spent four hours
every week on improvement activities.
What is the result? Both facilities are in the same city, have employees with
the same educational level, and pay roughly the same wage. Yet annual turnover
of associates in the first facility is 70 percent (which seems to be typical
in distribution centers) and there is significant management turnover as well.
Meanwhile, in the second facility, associate turnover is 1 percent and
practically no managers leave. When I asked managers and associates in the
second center why this should be, the answer was simple: "The work here is
always challenging because we are always solving problems using a method we
all understand. And we all respect each other’s contribution."
The differences continue: In my rough estimate labor productivity in the second
facility is about twice that of the first even with less automation. This is
partly because the first facility is constantly hiring and training new
employees while the second distribution center spends practically no time
on this task. In addition, all employees in the second facility are experienced
and working at the top of their learning curve. Large amounts of confusion
about what to do next and larger amounts of rework are eliminated.
Finally, in the second facility, quality as experienced by customers is higher
as well even though there is less internal rework. And the total amount of
inventory on hand to provide the next-day service that both facilities promise
their customers is also much lower in the second distribution center.
I trust you can guess which facility is a Toyota parts distribution center and
which facility belongs to a distribution firm stuck (like most) in the age of
mass production with command-and-control management methods but little
discussion of how employees can best do their jobs.
I also trust that all of us want to show respect for people. The challenge for
those of us in the Lean Community is to embrace and explain the true nature of
mutual respect for people – managers and associates – so all organizations
can move toward a new and better way of solving their problems.
Best regards,
Jim
Jim Womack
Founder and Chairman
Lean Enterprise Institute
Feel free to forward this message to suppliers, customers, or colleagues who
are implementing lean - or should be.
If this e-letter was forwarded to you, visit http://www.lean.org to subscribe.
Just click the "Join" button on the right to get a free subscription and access
to all the valuable content about implementing lean principles in production
and service value streams.
--
Tags:
人資
All Comments
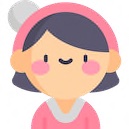
By Dora
at 2007-12-21T20:50
at 2007-12-21T20:50
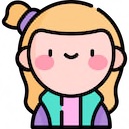
By Kumar
at 2007-12-23T02:14
at 2007-12-23T02:14
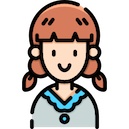
By Noah
at 2007-12-26T17:08
at 2007-12-26T17:08
Related Posts
窮忙一族 Working Poor
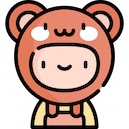
By William
at 2007-12-19T20:05
at 2007-12-19T20:05
(問卷)台灣人才競爭力及進修意向調查
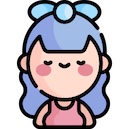
By Adele
at 2007-12-18T15:41
at 2007-12-18T15:41
Re: 就服乙級證照-放榜查詢
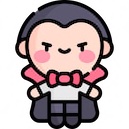
By Olga
at 2007-12-18T00:23
at 2007-12-18T00:23
人資長的五把績效鑰匙
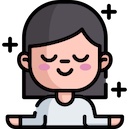
By Hazel
at 2007-12-17T11:35
at 2007-12-17T11:35
What Are HR Certifications Worth?
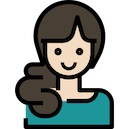
By Ida
at 2007-12-16T22:17
at 2007-12-16T22:17